Closed Die Forgings Manufacturer

Table of Contents
Introduction
An Indian forging company, SGEI Forgings Pvt.ltd. is a top manufacturer and supplier of a variety of high-quality closed die forgings and rolled ring forgings. We have been in business for more than 50 years, and during that period we have delivered with passion, quality, and the ability to complete an order on time. Customers value our items because they perform well. We provide a variety of products, including closed die forging and rolled ring forging.
In manufacturing, where strength, durability, and precision are essential, closed die forging consistently stands out as a superior process. If you have ever questioned how essential parts in items ranging from cars to aircraft are manufactured to endure tremendous pressure, the solution frequently resides in the complex but sturdy domain of closed die forging.We embody this precision at SGEI Forgings Pvt. Ltd. We are a prominent manufacturer of Closed Die Forgings, and we recognize the remarkable benefits this process provides. We are dedicated to producing top-quality forged components that enable industries to achieve new levels of success. We are the best Closed Die Forgings Supplier.
What Exactly is Closed Die Forgings
Picture that you want to manufacture a metal component that is both highly robust and extremely precise. While you could simply melt the metal and cast it in a mold, this method often results in small flaws and weaker structures. Closed die forging differs. Consider it this way: you take a metal piece, heat it to a certain temperature (making it malleable but not melted), and then put it between two shaped dies (the closed dies. We are the best Closed Die Forgings Provider.
These dies function like exact molds; however, rather than pouring in the metal, extreme pressure is used to compel the metal to occupy all the cavities of the dies. The metal’s internal grain structure is rearranged by this pressure, which is frequently applied by strong hammers or presses, resulting in an extraordinary degree of strength, toughness, and fatigue resistance.
Why Choose SGEI Forgings Pvt. Ltd
- Decades of Expertise: With more than 50 years in the industry, SGEI Forgings Pvt. Ltd. offers unmatched experience for every project. Our long-term presence in the market demonstrates our thorough understanding of forging processes, materials, and customer needs.
- Unwavering Commitment to Quality: At SGEI Forgings, quality is not merely a catchphrase; it is the basis of all our activities. We implement rigorous quality control measures at each phase of the manufacturing process—beginning with material selection and culminating with final inspection. Our in-house testing capabilities, which include advanced radiography inspections, guarantee that every component complies with the highest standards of integrity and performance.
- Precision Engineering: Our expertise lies in the production of closed die forgings that meet exceptional precision and tight tolerance standards. With our advanced tooling capabilities and skilled engineers, we can accurately realize even the most complex designs, minimizing the need for additional machining and saving you time and money.
- Extensive Skill Set: SGEI Forgings can cater to a variety of requirements, whether you need parts for the automotive, oil & gas, or general mechanical sectors. We utilize a range of materials, such as carbon steel, alloy steel, and stainless steel, to deliver solutions customized for your particular application.
- On-Time Delivery: We recognize that in the current rapid industrial climate, delivering on time is crucial. We guarantee delivery of your orders as promised and help you uphold your production schedules through our efficient manufacturing processes and dedication to deadlines.
- Customer-Centric Approach: SGEI Forgings is committed to fostering robust, cooperative relationships with our clients. From the first design phase to the final delivery, we collaborate closely with you to ensure that your specific needs and expectations are not only met but surpassed. Our expert team is always prepared to offer technical assistance and advice.
- Committed to Advancement: The forging sector is in a state of perpetual evolution, and we are evolving alongside it. To improve our capabilities and provide innovative solutions to our customers, SGEI Forgings is always investing in new technologies and processes.
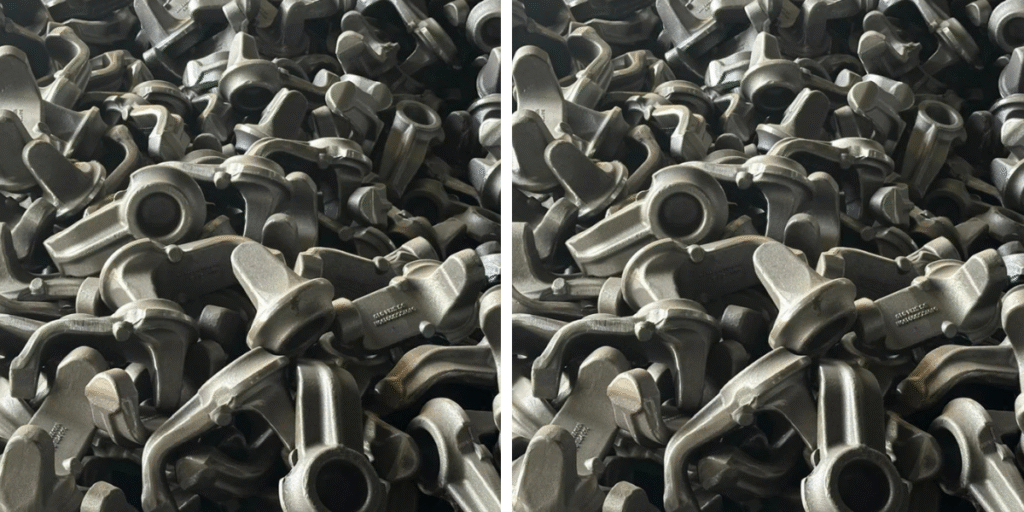
Applications of Closed Die Forgings
- Automotive Sector: Connecting rods, crankshafts, gears, axles, steering knuckles, wheel hubs essentially any vital part that undergoes significant stress and must be light yet extremely robust.
- Aerospace Industry: Components of landing gear, turbine disks, structural fittings, and additional parts that must endure severe temperatures and pressures while remaining lightweight. Safety is something we can’t compromise on here.
- Defense Industry: Military vehicles, weaponry, and equipment require components that can endure extreme conditions and tremendous stress. Forged components find extensive application in tanks, armored vehicles, artillery, and essential parts of firearms.
- Oil & Gas Industry: In the oil and gas sector, drilling equipment, wellhead components, valves, flanges, and high-pressure fittings must withstand corrosive environments, extreme temperatures, and immense pressures. Forged components offer the required trustworthiness and durability.
- Agriculture & Construction Equipment: Forged components are employed in the axles, gears, shafts, hydraulic cylinders, and other load-bearing elements of heavy machinery such as tractors, excavators, bulldozers, and cranes to guarantee durability and extended operational life.
- Railway Industry: Train wheels, axles, couplings, and numerous locomotive components experience tremendous forces and ongoing abrasion. Forged parts are crucial for ensuring the safety and reliability of railway systems.
- Power Generation: The strength and heat resistance of forgings are essential for components used in turbines, generators, and other machinery in power plants, including those for nuclear, thermal, and hydroelectric power.
- Marine Industry: Forged materials provide corrosion resistance and strength for propeller shafts, engine components, and various fittings used in ships and offshore platforms.
- Mining Industry: Components for mining machinery that are heavy-duty, like gears, shafts, and specialized tools, are frequently forged to endure the harsh and abrasive conditions of mining.
Table Specifications of Closed Die Forgings
Parameter | Specification |
---|---|
Product Type | Closed Die Forged |
Material Options | Carbon Steel, Alloy Steel, Stainless Steel, Aluminum |
Weight Range | 0.5 Kg to 150 Kg |
Process Type | Closed Die Forging (Impression Die Forging) |
Tolerance Level | ± 0.5 mm to ± 1 mm |
Surface Finish | As Forged / Machined / Heat Treated |
Heat Treatment Options | Normalizing, Hardening, Tempering, Annealing |
Testing Facilities | Ultrasonic Testing, MPI, Hardness Test, Dimensional Inspection |
Industries Served | Automotive, Oil & Gas, Railways, Aerospace, Construction, Agriculture |
Customization | Available as per customer design & drawing |
Certifications | ISO 9001:2015, IATF 16949 |
Advantages of Closed Die Forgings
- Unparalleled Strength and Integrity for Heavy Loads When faced with immense forces – such as those in a giant excavator arm, a massive wind turbine shaft, or essential components of an oil rig – sheer strength is imperative. Large closed die forgings offer.
- Enhanced Grain Flow: The process of forging aligns the internal grain structure of the metal with the contours of the component. This uninterrupted grain flow is vital for optimizing strength in large components, particularly in regions exposed to high stress, impacts, or vibrations. This indicates that the component is capable of enduring great stress without collapsing.
- Removal of Internal Flaws: The process of casting large parts can frequently result in internal voids, gas pockets, or structural inconsistencies. Through closed die forging, the intense pressure eliminates these flaws, yielding a material that is entirely solid and homogeneous. This is crucial for the safety and durability of heavy machinery.
- Improved Fatigue Resistance: Large components are frequently subjected to repetitive stress cycles. A large closed die forging’s microstructure refinement substantially enhances its fatigue resistance, allowing it to withstand numerous operational cycles without cracking or breaking, thereby greatly extending the service life of the machinery it is incorporated into.
- Enhanced Impact Resistance: In applications where sudden, severe impacts frequently occur (such as with mining or construction equipment), the superior toughness and impact resistance of large forgings are crucial in averting disastrous failures.
- Denser Material: The process of high-pressure forming yields a material that is denser and less porous than castings. This heightened density leads to improved resistance to wear, corrosion, and erosion—essential factors for components subjected to harsh environments.
- Uniform Material Characteristics: The material characteristics are exceptionally uniform from one end of the large forging to the other. For performance and reliability to be predictable especially in crucial structural components—this uniformity is vital.
Types of Closed Die Forgings
1. Automotive Forgings
- These forgings are used in the automotive industry for producing critical components such as gears, crankshafts, axles, connecting rods, and steering parts. They ensure high strength, wear resistance, and fatigue durability, making them suitable for high-performance vehicles.
2. Railway Forgings
- Forged components for railways include couplings, brake parts, axle components, and other safety-critical elements. Our railway forgings guarantee durability and reliability for the demanding conditions of railway operations.
3. Industrial Machinery Forgings
- Industrial machinery requires heavy-duty and robust parts. We manufacture closed die forgings like levers, shafts, flanges, and brackets for various industrial applications, ensuring long service life and high performance.
4. Agricultural Forgings
- Agricultural machinery parts such as tiller blades, plow parts, and connecting links are forged using closed die techniques to withstand continuous wear and tough working conditions in fields.
5. Defense and Aerospace Forgings
Components for defense and aerospace sectors demand exceptional strength, accuracy, and safety. Our forgings for these industries meet strict quality standards and precision requirements.
6. Construction Equipment Forgings
- Heavy-duty construction equipment parts like teeth adapters, clamps, and track links are produced using closed die forging to endure rigorous working environments.
Conclusion
As the world demands greater strength, reliability, and efficiency from its machinery and infrastructure, closed die forgings emerge as a fundamental manufacturing process. They provide unparalleled material integrity, exceptional mechanical properties, and cost benefits for mass production. We are the best Best Closed Die Forgings Manufacturer.
We at SGEI Forgings Pvt. Ltd. are committed to utilizing the complete potential of closed die forging. We are an industry leader due to our commitment to quality and innovation, as well as our demonstrated ability to produce high-performance large application forgings. We are convinced that our provision of the most robust and trustworthy components is helping to bolster and advance a variety of sectors, in India and around the world.