Closed Die Forgings Parts Manufacturer
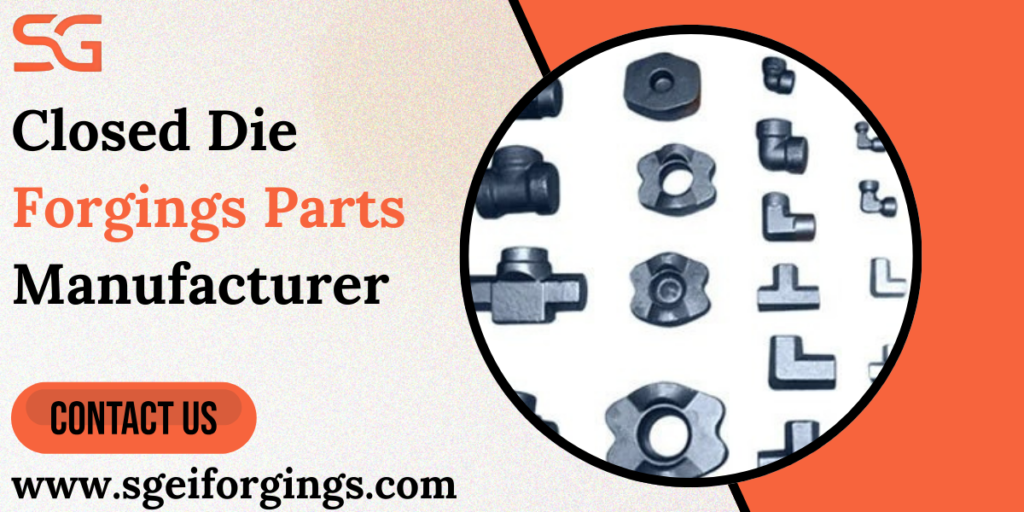
Closed Die Forgings Parts/Closed Die Forgings Parts Manufacturer/Closed Die Forgings Parts Supplier/Closed Die Forgings Components Manufacturer/Closed Die Forgings Manufacturer/
Table of Contents
Introduction
An Indian forging company, SGEI Forgings Pvt.ltd. is a top manufacturer and supplier of a variety of high-quality closed die forgings and rolled ring forgings. We have been in business for more than 50 years, and during that period we have delivered with passion, quality, and the ability to complete an order on time. Customers value our items because they perform well. We provide a variety of products, including closed die forging and rolled ring forging. We are the best Closed Die Forgings Parts Manufacturer.
One of the most sophisticated and effective techniques for producing metal parts that need to be extremely precise and strong is closed die forging. This method is perfect for creating complex shapes with enhanced mechanical qualities because it shapes metal by applying compressive force inside a die cavity. We will examine the closed die forging process, its benefits, its uses, and how SGEI FORGINGS PVT LTD is a top producer of premium closed die forgings parts in this blog.
What is Closed Die Forging?
In closed die forging, sometimes referred to as impression die forging, a piece of metal—typically a billet—is heated to a specified temperature before being inserted into a mould or die. The metal is compressed under tremendous pressure inside the die, which has a cavity shaped like the finished component. Compared to parts made using other techniques, this process produces parts that are more precise, robust, and durable.
Closed die forging allows complex shapes and tighter tolerances than open die forging, which allows the metal to be freely shaped between two dies. It is a cost-effective way to produce high-quality parts in large quantities because it also minimises material waste.
The Closed Die Forging Process
The following steps are commonly included in the closed die forging process:
- Material Selection: Selecting the right substance for the forging process is the first step. Depending on the final part’s desired properties, closed die forging frequently uses materials like steel, titanium, aluminium, and different alloys.
- Heating the Metal: Depending on the material, the selected metal billet is heated to a precise temperature, typically between 900°C and 1200°C. The metal flows more easily into the die cavities when heated because it becomes harder.
- Shaping in Dies: After the heated billet is inserted into the closed die, the metal is shaped by applying high pressure using a press. The die is made using the part’s final shape, guaranteeing that it is precisely reproduced.
- Cooling and Trimming: The part is cooled following the forging process, and any extra material—referred to as flash—is cut away. This stage guarantees that the finished product has the exact measurements and surface quality needed.
- Finishing: To improve its qualities and give it the desired look, the forged part may go through additional finishing procedures like machining, heat treatment, or coating.
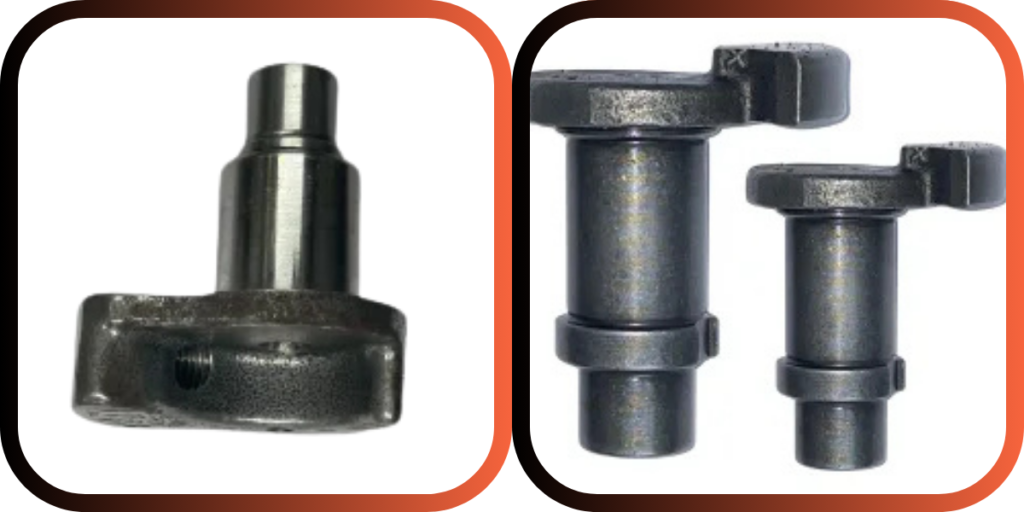
Advantages of Closed Die Forging
Compared to alternative manufacturing techniques, closed die forging has the following benefits:
- High Strength and Durability: The metal’s grain structure gets improved during the forging process, giving it greater density and durability. Parts with greater strength, fatigue resistance, and impact resistance are the result of this.
- Increased Precision: Closed die forging makes it possible to produce parts with complex shapes and tight tolerances that would be challenging or impossible to accomplish using other techniques, such as casting.
- Cost-Effective for Large Production Runs: The closed die forging process is more economical when producing large quantities of parts, despite the fact that the initial tooling costs may be high. It is perfect for mass production because of the speed of production and the decrease in material waste.
- Consistency: Every part made using the closed die forging process is guaranteed to have the same dimensions, form, and mechanical characteristics. For industries that need parts with exact specifications, this consistency is essential.
- Decreased Material Waste: Compared to other processes like casting or machining from solid stock, there is less material waste because the metal is shaped inside the die cavity.
- Versatility: A wide range of parts, from small, intricate components to large, heavy-duty parts used in industries like automotive, aerospace, and industrial machinery, can be produced using closed die forging.
Applications of Closed Die Forging
Many different industries use closed die forging, and each one has different requirements for the parts it produces. Among the most important uses are:
- Automotive Industry: Wheels, suspension parts, gearbox systems and automobile engines frequently use forged parts. Parts made by closed die forging are capable of resisting the extreme strains and requirements of the automotive industry.
- Aerospace Industry: Forged parts are used in the aerospace industry for structural elements, landing gear, and aircraft engines. Closed die forging’s high strength-to-weight ratio makes it perfect for aerospace applications.
- Oil and Gas Industry: Closed die forging is used to create parts that need to endure high pressure and harsh environments, like flanges, fittings and valves.
- Industrial Machinery: Closed die forging is used in the production of many parts for industrial machinery, such as gears, shafts, and couplings. To survive the heavy loads and continuous wear they experience, these parts must be robust and permanent.
- Military and Defence: Closed die forging is used in the defence sector to create dependable, high-strength parts like ammunition casings, armour, and gun parts.
- Energy Sector: Closed die forging is frequently used to create parts used in power generation, such as steam valves and turbine blades.
Why Choose SGEI FORGINGS PVT LTD: Best Closed Die Forgings Parts Manufacturer
One of India’s top producers of closed die forgings parts, SGEI FORGINGS PVT LTD provides a large selection of forged goods that satisfy the strictest quality requirements. We are the best Closed Die Forgings Components Manufacturer. The following justifies selecting SGEI Forgings for your upcoming project:
- Modern Manufacturing Creation
SGEI FORGINGS PVT LTD has a modern manufacturing facility with modern machinery and technology. Every part is produced to perfection because the facility is built to manage the complete forging process, from billet heating to final trimming. - Knowledge and Experience
SGEI Forgings has years of experience in the closed die forging parts business and has a strong grasp of how to create forged parts of superior quality. Each product is guaranteed to meet the necessary specifications and quality standards by their team of highly qualified engineers and technicians. - A Large Selection of Materials
Carbon steel, alloy steel, stainless steel, and other high-performance alloys are among the materials that SGEI Forgings works with. Because of their flexibility, they can manufacture forged parts for a wide range of industries, such as the automotive, aerospace, industrial, and defence sectors. - Accuracy and Excellence
Quality is the top priority at SGEI Forgings. To guarantee that it satisfies the necessary tolerances and mechanical qualities, every forged part is put through strict quality control procedures. To ensure the highest quality standards, the company employs sophisticated testing techniques like dimensional inspection, bending testing, and hardness testing. - Customised Solutions
Custom forging solutions that are suited to each client’s particular requirements are SGEI Forgings’ area of expertise. SGEI Forgings can offer a solution that meets your needs, whether you require a large quantity of standard parts or a small batch of high-precision components. - Reasonably Priced
SGEI Forgings provides affordable solutions without sacrificing quality. The business is able to provide competitive pricing on all forged parts because of its effective production procedures and large-scale manufacturing experience. We are the best Closed Die Forgings Manufacturer. - Prompt Delivery
SGEI Forgings is aware of how important prompt delivery is in the fast-paced manufacturing industry. They guarantee that your forged parts will always arrive on schedule thanks to an effective supply chain and a dedication to meeting dates.

Conclusion: Closed Die Forgings Parts Manufacturer
A very efficient technique for creating precise, solid, and durable metal parts is closed die forging. The method is preferred for sectors like automotive and aerospace because it provides a number of benefits, such as increased strength, accuracy, and cost-effectiveness.
At the forefront of the closed die forging sector, SGEI FORGINGS PVT LTD provides premium forged parts for a variety of uses. For all of your closed die forgings parts requirements, SGEI Forgings is your reliable partner because of its dedication to accuracy, excellence, and client satisfaction. We are the best Closed Die Forgings Parts Supplier.
You need look no farther than SGEI FORGINGS PVT LTD for a trustworthy closed die forgings parts manufacturer. Get in touch with us right now to get the specifics of your project and allow us to offer you the best forging solutions available.